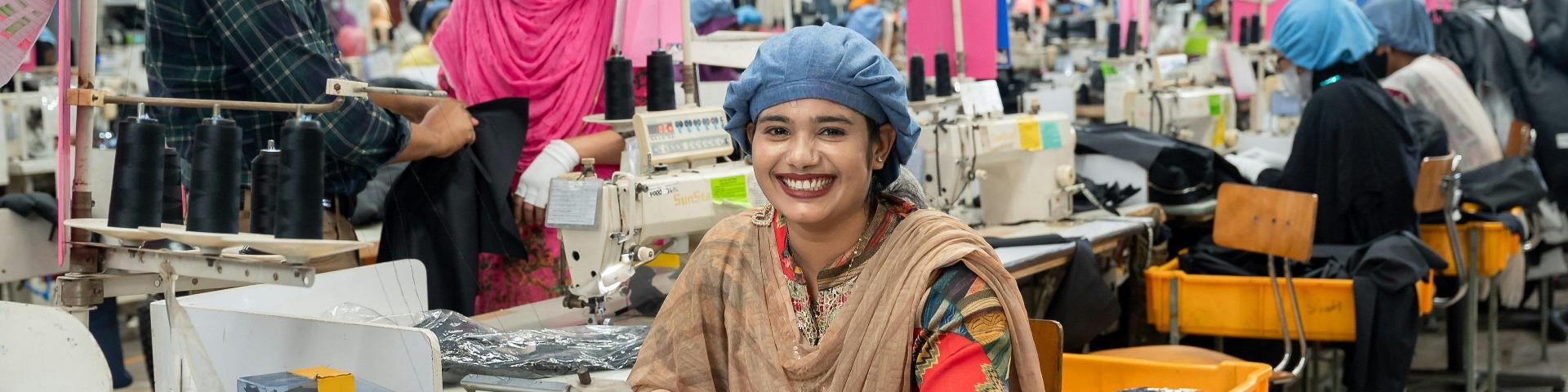
7 tips on how to increase efficiency in an apparel factory
Maximising efficiency in your factory is crucial for increasing profits and staying competitive. Efficiency is not about operators working faster – it involves reducing wasteful processes, minimising mistakes and lowering costs. A well-organised and efficient production process leads to lower inputs (including materials, energy and water), higher output, less waste, better quality, better overall competitiveness and happier employees. This report explores different ways to boost efficiency in production, training, quality control and management.
Contents of this page
1. Understand the apparel manufacturing process
An apparel manufacturer producing an order for a buyer is selling an amount of garments for a certain total price. In essence, however, every apparel manufacturer is selling production capacity: the total minutes that you have available for operators to work on your machines with available materials to make apparel items. If you save on these minutes, you can lower your prices or increase your profit. Or you can do both.
Increasing efficiency while offering flexibility
The easiest way to increase your efficiency is to produce larger orders. This way you do not have to change much in your production line, how your operators work, or any other part of your operation. It makes sourcing materials and planning easier. You do not have to change the production line so often, and operators can focus longer on making the same or similar styles. This is why many apparel manufacturers prefer big volume business.
On the European market, however, there are not many buyers that require big volume orders. Most buyers require small MOQs and short lead times (in addition, of course, to high quality, a good price and a high level of compliance with environmental and social standards). If you want to be competitive in Europe, you need to be flexible. The key challenge therefore is to increase your efficiency while staying flexible.
Key stages in production
When thinking about increasing efficiency, many apparel manufacturers focus on their operators and their machines. They believe that efficiency will grow if the operators work faster and the machines are set up smartly. This is only partly true. Just as important for increasing your efficiency is planning and monitoring. Each step of the apparel-making process needs to follow logically after another, and all teams need to work together seamlessly. It is therefore important to map all the production steps in your factory.
Table 1: Typical production steps in an apparel factory
Production stage | Details |
Design and development | Concept creation, fabric and trim selection, prototyping |
Pattern-making | Creating patterns, grading for different sizes |
Sampling | Prototyping, fitting, adjusting and approval |
Sourcing | Sourcing fabrics, trims and accessories, testing |
Production planning | Costing, creating a production timeline, factory allocation |
Cutting and preparation | Fabric inspection, spreading and cutting, label preparation |
Sewing and assembly | Stitching, using specialised machinery for different components (including buttonholes, embroidery, prints), quality control |
Finishing | Pressing, ironing, trimming, attaching labels, tags |
Quality control | Final inspection for defects, safety compliance |
Packaging | Folding, polybagging, adding hangtags, barcodes, QR codes, boxing |
Distribution and logistics | Shipping, inventory management |
After-sales | Returns, repairs, feedback collection |
Common efficiency challenges
Issues that lower your efficiency can occur at every stage of production. That is why you should focus on more than just your operators and machinery. To eliminate inefficiencies, take your entire operation into consideration. Perhaps you recognise some of the inefficiencies listed in the table below.
Table 2: Common efficiency challenges in every stage of production
Production stage | Common efficiency challenge |
Design and development, Pattern-making, Sampling | Miscommunication leading to incorrect specifications or missing details can disrupt efficiency, just as poor internal alignment between design, production and merchandising teams, and a lack of integration between Enterprise Resource Planning (ERP) systems, design software and production management. If the quality of the product is sensitive, this may result in slower production, for instance the use of soft fabrics resulting in seam slippage. |
Sourcing | Poor sourcing and fluctuating material prices can lead to delays in fabric or trim deliveries, material shortages and rising costs. Quality issues may require re-sourcing. Starting production without the complete inventory of the different elements, including fabrics, accessories, trims, labels and packaging materials, always leads to delays. |
Production planning | Inaccurate demand forecasting and capacity mismatches can lead to overproduction, stock shortages or delays. |
Cutting and preparation, Sewing and assembly, Finishing | Poor cutting or fabric handling results in lower quality, higher rejection rates and thus unnecessary loss. Lack of skilled employees for complex tasks, high turnover rates and training needs can reduce efficiency. Complex styles including different handlings such as embroidery or printing may need to be outsourced, which can disrupt your timeline. Outdated machinery, poor maintenance (breakdowns) and low automation rates (lots of manual labour) can also lower efficiency. |
Quality control | Inconsistent quality checks and high defect rates can seriously reduce efficiency. Every piece that needs to go back to the start of the production line disrupts the entire production timeline. If the buyer’s acceptable quality level (AQL) does not allow for any mistakes, this will slow production. |
Packaging | Material shortages, incorrect sizes or designs, poor quality, incorrect or missing barcodes or tags, too much and/or inaccurate manual labour (folding, tagging, packing) and a disorganised warehouse can slow production. |
Distribution and logistics | Over-purchasing ties up capital and under-purchasing leads to a lack of materials and thus a delay in production. |
After-sales | High return rates due to issues with size, fit, design, quality and mislabelling, plus poor communication and poor inventory management can disrupt efficiency and lead to rising costs. |
2. Identify bottlenecks in the workflow
Identifying bottlenecks and inefficiencies in an apparel factory is crucial for improving productivity, reducing costs, meeting delivery deadlines and keeping your buyers happy. A systematic approach helps you pinpoint where delays or waste occur, which will make it easier to optimise your production process.
How to identify inefficiencies
Any attempt to increase efficiency should start by collecting data. This does not require a huge investment in state-of-the art technology. It is true that highly digitised apparel factories may utilise expensive software, machinery, materials and production lines equipped with QR codes, RFID chips, intelligent sensors and cameras connected to computer-controlled machinery using artificial intelligence (AI). However, gathering data can start simple: by inspecting your factory floor with a clipboard, pen and stopwatch in hand.
- Measure how long each step in production takes, including transport within the factory;
- Record waiting periods between operations. How many employees are idling and for how long;
- Record machine downtime, defect percentage, material waste and on-time delivery rate.
A value stream map can help you visualise how materials and information flow through your factory. By using a Gantt chart or the critical path method you can compare planned timelines with actual timelines for each production step.
Tips:
- Track movement and reduce unnecessary steps in the production line. Create a clear workflow where each step follows smoothly after another;
- Ensure all materials are available before production starts;
- Check this blog article on The Fashion Workstore about creating a critical path.
3. Optimise your workflow
Optimising your workflow means organising your production in such a way that each step follows logically and smoothly after another and takes as little time and effort as possible. It also means that unnecessary steps in your workflow should be eliminated. This way you will save time and costs. If done right, it will result in a better-organised workplace, where employees can have more of an influence on the way they work at the factory.
Production line setup
How the space between tables and production lines is organised is crucial to keeping your factory running efficiently. There are different ways to do this. A U-shape in which operators can easily move between workstations will typically provide higher flexibility and is suitable for producing smaller orders with more complex styles. Straight production lines are suitable for producing large volume orders. If your factory does both, consider setting up two different, clearly separated production lines.
The figures below show the importance of having enough space around the workplace to achieve higher productivity and to have better control of what happens in the production line.
Figure 1: A U-shaped production line
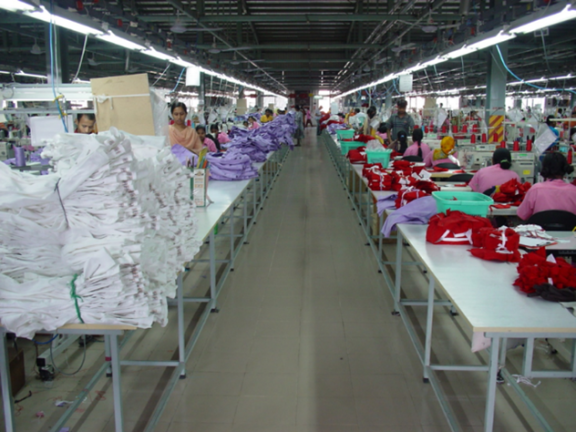
Source: Forward in Fashion
Figure 2: A straight production line
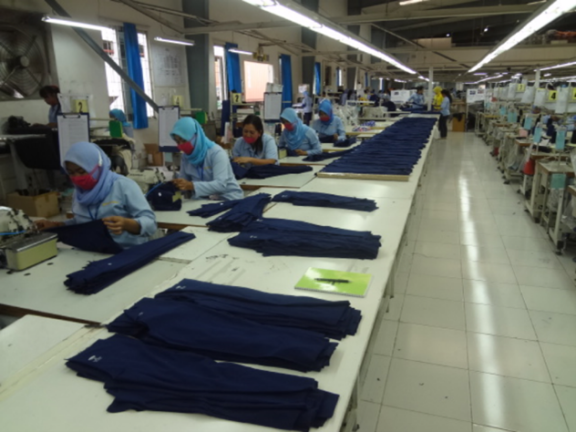
Source: Forward in Fashion
Tips:
- Leave enough space between tables for easy movement;
- Keep workstations organised and clean;
- Check out the Japanese 5S methodology. It offers a relatively easy guidebook to organising your factory floor and keeping it clean and tidy.
Minimise mistakes
One big reason for low efficiency is poor quality assurance (QA) and quality control (QC). If these are not well-organised, mistakes can happen, leading to wasted time and materials. To ensure consistent quality you need to follow clear steps at every stage of production. This includes checking materials before use, inspecting products during production, and reviewing finished items before packing.
Employees should be trained to spot defects early, and a system should be in place to fix problems quickly. Using checklists, quality reports and regular inspections can help maintain high standards. Good QA and QC improve efficiency by reducing rework, saving time and ensuring happy buyers.
Tips:
- Track how many mistakes are made during a production run. What kind of mistakes? What are the underlying reasons for the mistakes? How much extra time does it cost to solve the mistakes;
- Track defect rates at each production step: identify stages with the highest rejection rates;
- Investigate whether defects are caused by human error, machine malfunction or poor material quality.
Material inspection
Fabrics need to be inspected for defects, and trims need to be tested to guarantee standards are met. Do not inspect only a sample, for instance 10% of the fabrics. Check all materials so you will know the actual information that is useful for follow-up operations. All fabrics and trims must be checked immediately after arriving. This gives time to respond if a piece of material is not up to standard.
All fabrics must be inspected 100% to get the following information about each roll:
- Usable width;
- Shade;
- Shrinkage;
- Usable fabric length;
- Number of defects.
Mark each defect with a sticker. This will help find the defective parts during panel checking. The defective parts must be re-cut immediately and joined to the bundle. This will reduce the number of defective pieces (second quality) and lessen disruptions in the sewing and finishing workflow. All data found must be marked on a sheet and on the roll. The data indicates that the spreading can be planned, which is a precondition to save fabric and time.
Having exact data gives you the possibility to file a claim with the supplier if the number of defects is higher than the agreed tolerance.
Do not forget to check the accessories. Trims that do not comply with quality standards will have a major impact. End customers will complain and money will have to be reimbursed, resulting in a decrease of profits or even loss.
Tips:
- Conduct a 100% fabric inspection, not just 10%;
- Use a tracking sheet to log production mistakes. A tracking sheet is an overview of every step in the production of an apparel item, from cutting to sewing steps and packing. This can be done by making a list in Excel of all the production steps. Write down any mistakes you encounter during each production step;
- Train employees to identify and report defects quickly.
Fabric storage
After fabric inspection the rolls must be stored, ready to work, in shelves according to the requirements of the cut order. The person who stores the fabric in the warehouse on the movable trolley must join the marker with the fabric; otherwise, moving the trolley to the cutting room is not allowed. For easy coordination between the fabric/accessory store and the cutting room, both departments should be managed by the same person.
Make sure that your fabric storage room is clean and well-ventilated and that a barcode system is in place. Keep your fabrics in racks.
Tips:
- Keep fabric on shelves or racks, never on the floor;
- Use barcode systems to track fabric movement;
- Ensure proper ventilation in storage areas.
Fabric cutting
The size and quality of work tables are very important for improving efficiency. If tables are too small or not strong enough, employees may struggle to handle materials properly, causing delays. For factories that produce large quantities, investing in an automatic fabric spreader and laser cutter is a smart choice. These machines work faster and more accurately than manual cutting, reduce mistakes and save time. Manual cutting is slower and can lead to errors, which may increase material waste.
To further improve efficiency, factories can use a barcode or RFID system to track employee performance and fabric usage for each production order. Every time an operator opens a bundle of cuttings for processing at the sewing line, the barcode or RFID chip is scanned, making it possible to track in real time how many bundles any operator processes in a given amount of time.
This helps improve planning, reducing waste and ensuring smooth operations. Regular maintenance of cutting machines and proper training of employees can also enhance productivity and product quality.
Figure 3: An automatic spreader
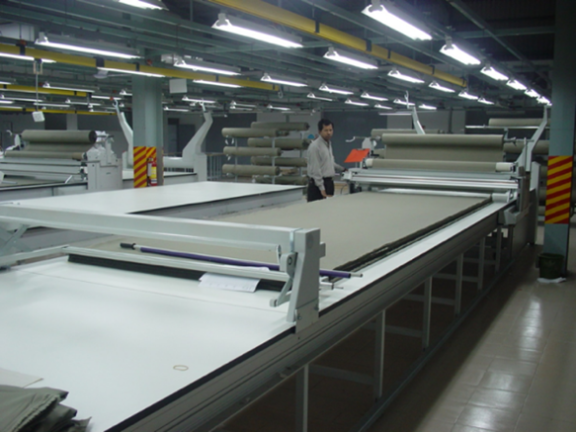
Source: Forward in Fashion
Figure 4: Manual cutting
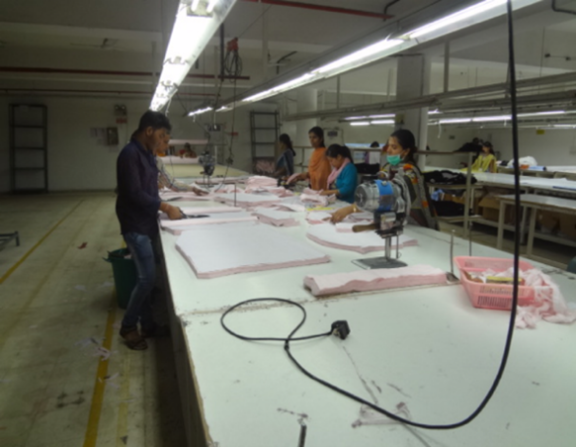
Source: Forward in Fashion
Tips:
- Do not store fabric under a table or elsewhere on shelves together with finished cut garments. The only exception is for styles with parts that are embroidered or printed;
- Use automatic spreaders and cutters for high-volume production;
- Avoid manual cutting where possible to reduce errors;
- Organise a clear workflow between storage, cutting and sewing.
Manual spreading
Many apparel factories still spread fabrics manually with a single table system. This blocks the workflow because employees cannot work continuously.
Figure 5: Manual spreading
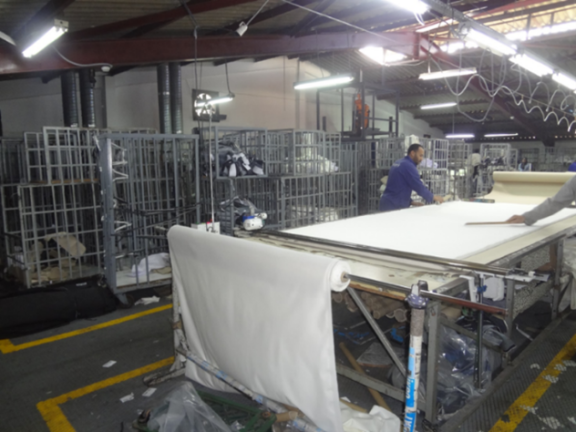
Source: Forward in Fashion
When taking fabric from storage, sort it by colour, shade and usable width before placing it on movable racks. These racks help transport the fabric easily and quickly to the spreading table without confusion or delays.
For better efficiency, the spreading process should use two tables. While fabric is being spread on table A, the fabric on table B can be cut, checked and bundled. This setup saves time and reduces unnecessary movement of materials. To keep the workflow smooth, one rack should always be in use while another is ready for unloading. Employees should follow a clear system to avoid delays and mistakes. Regular checks on fabric sorting and transport can help improve speed and accuracy in production.
Figure 6: Input trolleys in front of the spreading table
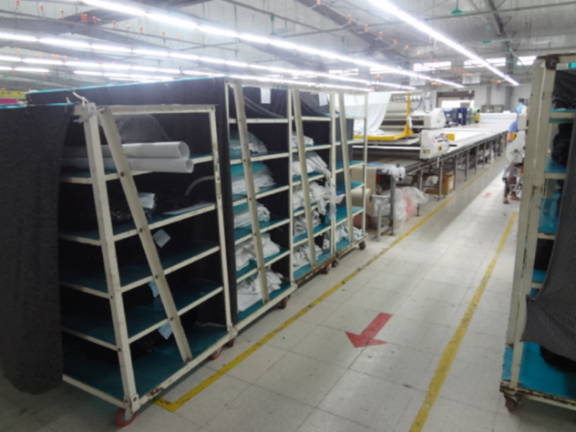
Source: Forward in Fashion
Figure 7: Spreading the fabric
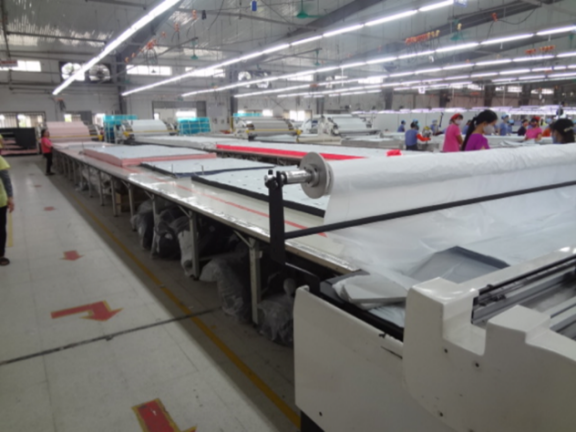
Source: Forward in Fashion
Figure 8: Numbering, panel checking and bundling
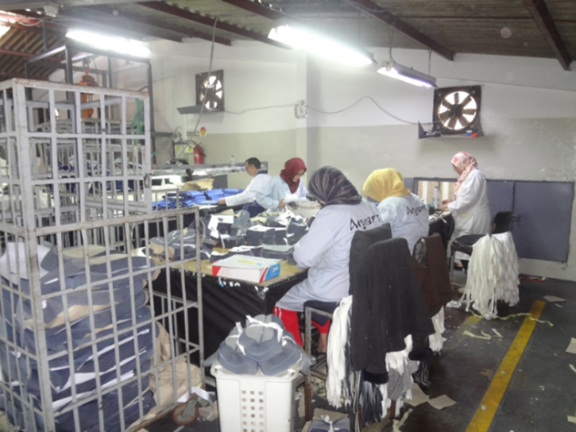
Source: Forward in Fashion
As soon as the first fabric pieces are cut, employees should start numbering them. The same person that checks the panels should also create the bundles. Each bundle must include all the necessary parts of the garment, and the details should be written on a tag attached to the bundle. Next, the bundle is placed on a ‘baker’ trolley for easy transport. The trolley is then moved directly to the sewing department or fusing machines, ensuring a smooth workflow.
If some parts need embroidery, they should be stored separately on shelves to avoid confusion. To improve efficiency, employees should follow a clear process for bundling and labelling. Regular training on handling bundles correctly can help reduce errors and speed up production. Using barcode labels or digital tracking can also make it easier to manage materials and avoid missing pieces.
Figure 9: Bundles ready for loading
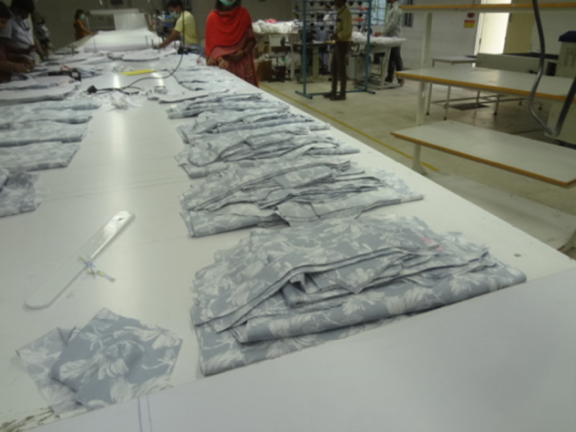
Source: Forward in Fashion
Figure 10: Bundles loaded on baker trolleys, ready to transport to sewing
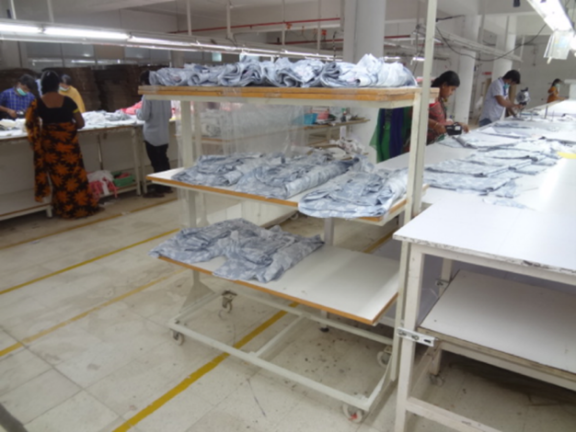
Source: Forward in Fashion
Balancing the sewing line
If one workstation in an apparel production line takes significantly longer than others, it creates a bottleneck, slowing down the entire production process. Evenly distributing work across all operators and machines in a production line is called ‘balancing the line’. The purpose is to ensure a consistent workflow, maximise efficiency and minimise idle time or bottlenecks.
Before you can balance the line, you need to do a time study using the principle of Standard Allowed Minutes (SAM). SAM can be defined as the time it takes to properly produce a certain type of garment. The operation cycle is broken down into operation steps (see above) and observed time is captured per element, including transport within the factory. Larger factories often use PMTS (Principal Member Technical Staff) software to help them measure the SAM, but this exercise can also be done with a stopwatch and a clipboard.
To do this, take the following steps:
- Select the operation or workstation you want to analyse first;
- Document the current method of working;
- Use your stopwatch to record the time each operation cycle takes;
- Assess the operator’s speed compared to a standard employee’s performance.
Calculate your line efficiency by using this formula:

Once you have done this, you can analyse inefficiencies and:
- Distribute work among operators based on their skill level and the SAM of each task;
- Identify which operators fall behind in their work, causing others to wait;
- Split tasks that take too long into smaller ones or assign more operators to a task;
- Create buffer zones (small storage areas) between critical steps to prevent delays.
Tips:
- Check the CBI study on cost price calculation to learn more about Standard Allowed Minutes (SAM);
- Assign employees based on their experience level for better balance. Train employees to be skilled in multiple tasks to balance the workload and increase flexibility.
Absenteeism
In any department, always make sure you have 5% extra personnel to replace absent employees. This is especially important for sewing, which is the most labour-intensive department. At the beginning of the work shift, these workers must be assigned where needed.
Tips:
- Keep extra employees available to replace absent employees;
- Distribute work fairly to avoid stress and burnout;
- Monitor attendance patterns and address issues early.
In-line inspection
Train your employees to report any defects to the line manager as soon as they notice them. If an employee does not report a defect, production will continue and the mistake will only be found later. This will require extra time to fix, slow down production, increase costs and reduce overall profit. The line manager must collect the defective pieces immediately and send them back for quick repairs to the workstation where the mistake happened.
Once the garment is fixed, it should be placed back into the bundle. This is important because only complete bundles should move to the finishing department.
To maintain quality, a random quality control system should be introduced, such as Acceptance Quality Limit (AQL). This means checking products at different points in production without a fixed schedule. If more defects are found, the number of checks should increase to prevent further mistakes. This system helps monitor every workstation and ensures that employees stay alert about quality. It also makes the quality status visible to everyone in the production line, helping the factory maintain high standards and improve efficiency.
Tips:
- Train employees to understand the importance of reporting defects immediately;
- Repair defective items in the same production line to avoid extra work;
- Conduct random quality checks to ensure consistency.
Temporary storage
Before the garments arrive at the finishing department they should be loaded on ‘baker’ trolleys or stored by packing requirement (ratio, single, bulk).
Tips:
- Assign individual workspaces to packers;
- Follow customer packing requirements carefully.
Ironing
Ironers should be trained on how to use the iron in the correct way based on a coordinated movement. This creates consistent quality in finishing. They also need to understand when and how to use steam or pressure. By working with ‘baker’ trolleys or stands as a transportation system, there will be more space on the ironing tables and the ironed pieces can be placed properly. Each checker after ironing must have their own, stationary and individual workplace.
Tips:
- Use systematic movement for consistency;
- Provide proper space for ironed garments;
- Consider using automated pressure machines;
- Consolidate your boiler machines to save energy.
Figure 11: Ironing workplaces for pants
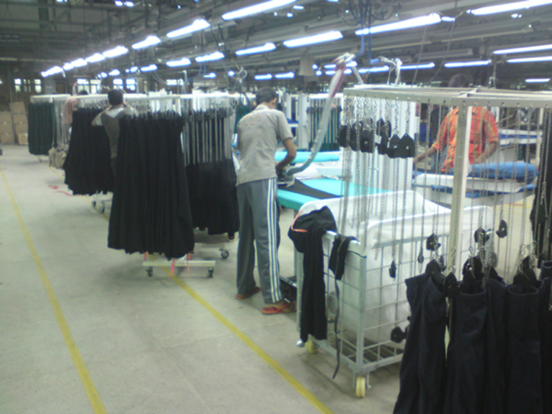
Source: Forward in Fashion
Figure 12: Ironing workplace for knits
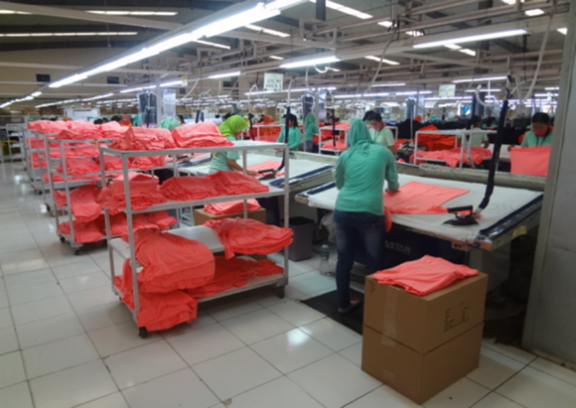
Source: Forward in Fashion
Figure 13: Inspection after ironing workplace
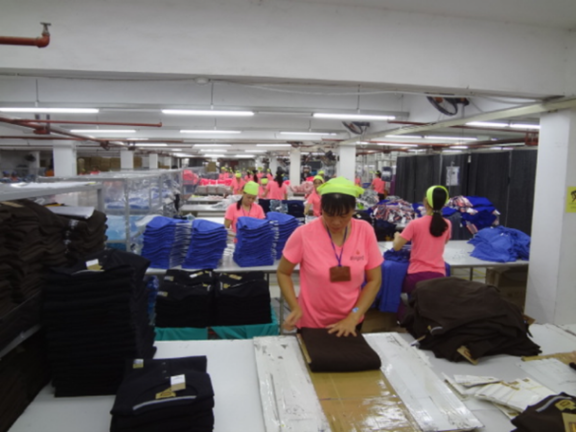
Source: Forward in Fashion
Folding and packing
Each employee must have their own individual workplace and follow all working steps, including putting the garments into a box. It is important that each employee have enough space around the workplace to achieve high productivity.
Figure 14: Folding
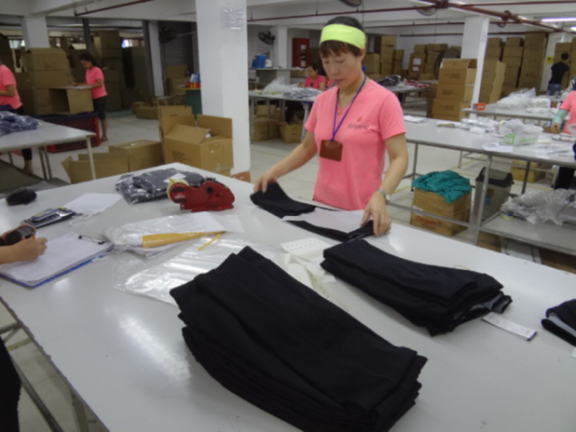
Source: Forward in Fashion
Final inspection
When production is finished it needs to be inspected to make sure it complies with the buyer’s AQL standard. Final production can be inspected at random or piece-by-piece. Be aware that a piece-by-piece inspection will reduce your profit and will cost time. The average repair quota is 3%. Always try to find out how a defect happened and how to prevent it, especially in case of structural defects.
LEAN manufacturing principles
Many factories that want to improve efficiency follow the LEAN manufacturing philosophy, which involves several principles that have been touched upon in this study. LEAN maximises value by minimising wasteful processes and activities that do not add value, such as excess inventory, waiting time, or defective materials and products. LEAN manufacturing uses principles like Just-In-Time production, continuous improvement (Kaizen) and standardised work.
LEAN can serve as a guidebook for adjusting your production. The basic principles include:
- Identify what your buyer values most (quality, speed, price, service, sustainability);
- Focus on eliminating all production steps that do not add any of these values;
- Map the value stream (see above);
- Balance the line (see above);
- Produce only what is strictly needed, focus on small batches, and use Kanban boards or digital tracking systems to signal when new materials are needed at the production line;
- Develop Standard Operating Procedures (SOPs) for each production step to ensure consistent quality and performance;
- Improve continuously (Kaizen) by involving employees to make suggestions for improvements and to monitor and discuss performance regularly;
- Implement in-line quality checks;
- Use visual tools such as posters, laminated brochures, whiteboards or TV screens with instructions using both text and pictograms throughout the factory to improve workflow and to communicate targets and performance metrics.
Tips:
- Read the CBI study on buyer requirements to learn what European apparel buyers value and require from you;
- Read the CBI study on how to do business with European buyers to learn how to join an export coaching programme (by CBI for instance). These programmes can help you find and employ experts in LEAN manufacturing;
- Kanban is another frequently applied and relatively easy reflexive management system focused on optimising production flow on the factory floor. The basic principles are explained in this article from Apparel Resources.
4. Consider automating your production line
Many people believe that automated cutting and sewing machines increase production speed. In fact, it mostly improves efficiency, by increasing product quality and enabling employees with less experience to perform complicated movements.
If you want to invest in automated machinery, companies like Kuris and Zünd provide the latest technologies in digital cutting techniques, like 3D cutting. Others, like Brother (USA), Juki (USA) and Jack (China), provide sewing machines that can be digitally linked to a smart factory software system, integrating the cutting and sewing department and optimising efficiency by balancing the line. Some factories also use QR/barcode tools to measure the time each process or employee takes.
Do not underestimate how complicated it is to install automated machines properly. Luckily, machinery suppliers will often provide technical support on site. This means they will send their experts to your factory to install or upgrade software and hardware. They can also help you integrate the machinery in a smart factory (software) system that lets you measure and improve the performance of your production line. This includes training your staff on how to properly operate and maintain the machines and software.
For more neutral (and usually more general) advice on apparel technology and innovation, try connecting with local institutions. Many production countries have organisations connected to industry associations, universities or technology hubs that can support you in automating the production process. For example:
- Centre Technique du Textile et de l’Habillement (CTTH) in Morocco;
- Ethiopian Institution of Textile and Fashion Technology (EITFT);
- Garment Design Training Services (GSC) in Jordan;
- Industrial Modernisation Centre (IMC) in Egypt;
- La Fédération Tunisienne du Textile et d’Habillement (FTTH) in Tunisia;
- National Institute of Fashion Technology (NIFT) in India.
Figure 15: An automated sewing machine by Juki
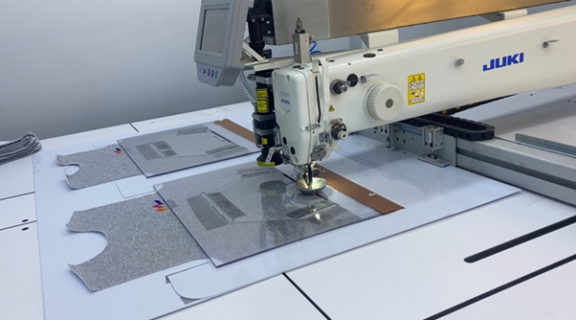
Source: Forward in Fashion
Tips:
- Watch this short video on YouTube by Juki (sewing polo plackets) and Richpeace Group (automatic sewing machine for attaching zippers) to get an idea of the type of production processes that can be automated;
- Invest in barcode systems to measure employee performance. Companies like WFX and Coats offer manufacturing software, like barcode technology, that can be used to track the flow of materials through the production process. You can easily book a demo online to get free advice on the benefits and use of such systems;
- Start with small automation steps, such as automated cutting, and expand over time to other departments.
Machine maintenance
Broken machines cause huge productivity losses in the average apparel factory. Maintaining your machines is therefore crucial. It is the responsibility of the production manager to provide employees with perfectly maintained and operational machines. Each machine must be inspected before handover. By introducing a performance/efficiency control system the lost time caused by bad machines is highlighted.
Tips:
- Inspect machines regularly;
- Fix or replace faulty machines immediately;
- Train employees to report issues quickly.
5. Train your employees for efficiency
Since apparel production is still centred around manual labour, training your employees is essential to achieve high efficiency. Workers are more productive when processes are streamlined, unnecessary tasks eliminated and mistakes minimised.
Workforce training and development
Factories often have new employees joining every month. Before these employees start working on the main production line, they need proper training in skills and work speed. Without training, they may slow down production and make mistakes. It is best to train new employees in a separate training area. This helps them learn without affecting the main production process.
Training should include machine use, work methods and quality control. Supervisors should guide new employees and check their progress. A step-by-step training plan can help employees improve faster. Using experienced employees as mentors can also make training more effective. Good training reduces mistakes, increases speed, and helps new employees feel more confident in their jobs.
Tips:
- Let high-performing people train others. The easiest step to improve efficiency is to have your workers learn from each other’s mistakes and strong points;
- Make it easy for your employees to express and share ideas for improvement, for instance by installing an ideas box.
Employee happiness
Keeping your employees motivated and happy is crucial to maintaining efficiency. A big challenge for the apparel industry, however, is to find motivated employees in the first place. Many young people are not as keen on working in apparel manufacturing as older generations. Your focus should therefore be on keeping existing employees happy and creating a working environment that meets the expectations of younger generations.
Financial rewards are often used to boost motivation and productivity. Paying your employees a competitive wage is crucial for keeping them happy. Offering bonuses based on effort and personal results can also help. However, being an attractive employer also means giving employees a sense of control and influence, pride, recognition, and a family feeling. Additionally, providing secondary benefits such as daycare and health insurance can increase employee loyalty.
Tips:
- Interview each employee once a year. Discuss not only individual performance but also their personal situation, needs, talent and ambition. Invest in your employees’ personal development and career growth within the organisation;
- Invest in yearly activities to connect people from all layers within the organisation.
Incentives
Based on SAM, individual performance and efficiency checks for each workplace should be introduced, from fabric inspection to packing. This will also be the basis for cost control. Pay your employees partially based on individual incentives.
6. Monitor efficiency improvements
Monitoring efficiency improvements in an apparel factory and acting upon the data is essential to keeping up your performance. Your productivity will fall, costs will rise, and quality standards will drop if you do not keep track of data.
Key Performance Indicators (KPIs)
Monitoring your performance requires the development of Key Performance Indicators (KPIs). These are goals you set for yourself to which you compare data on your current performance.
Relevant KPIs for an apparel factory include:
- Line efficiency (percentage);
- Output (number of garments produced per shift or day);
- Defect rate (percentage of defective items);
- Employee productivity (pieces produced per hour per employee);
- Machine utilisation rate (percentage of time machines are operational).
Tools for monitoring progress
Gathering data can be done using simple tools: a clipboard, a pen and a stopwatch. If you want to invest in software, there are plenty of options, like integrated Enterprise Resource Planning (ERP) systems, Product Lifecycle Management (PLM) systems, and specific software programmes for anything from stock management, order management and HR management to Customer Relationship Management (CRM).
Automated machinery, including digital cutting techniques and sewing machines linked to a smart factory software system, can monitor progress for you. Results can be shared in real time via tablets or screens on the factory floor. Factories also use QR or barcode tools or radio-frequency identification (RFID) chips to track items and measure the time each process or employee takes.
Tips:
- First try to optimise your production efficiency with the means you already have available in your factory (expertise, machinery, factory set-up, software);
- Invest in Enterprise Resource Planning (ERP) software to integrate your planning, inventory, sales, marketing, finance, human resources, and more. Check review platform SoftwareAdvice for a (non-exhaustive) overview of available ERP systems for the apparel industry.
7. Learn from best practices
In every factory there is room for improvement. If you want to see for yourself what an efficient factory set-up looks like, you can try to learn from peers by contacting your apparel sector association or joining an export coaching programme.
Best practices
- Sun Tekstil in Turkey is a good example of a vertically integrated, highly automated and highly efficient apparel factory. Their website features a film with images from inside the factory, giving a good impression of their well-organised factory floor layout. The company is known for its use of AI to optimise production;
- Jerash Holdings in Jordan is a highly automated apparel factory. The company improves efficiency by using automated cutting and stitching machinery and a digital printer.
Further reading
The CBI study ‘Tips to go digital’ can help you with finding and implementing the right tools to automate your factory and improve performance.
The CBI study ‘How to calculate the cost price of an apparel item?’ provides tips on how to calculate and reduce costs in your production.
FT Journalistiek carried out this study in partnership with Giovanni Beatrice on behalf of CBI.
Please review our market information disclaimer.
Search
Enter search terms to find market research